Zühlke
Zühlke takes initiative to cut carbon emissions for Bystronic
Bystronic and Zühlke share a common belief that sustainability is an opportunity to improve business. Thatʼs why the two partners joined forces on a transformation journey to significantly reduce emissions of bending and laser cutting systems, to foster decarbonization for their clients and to set a pioneering example of sustainable business in the sheet metal processing industry.
The collaboration between Bystronic and Zühlke is combining sustainability and profitability, resulting in actionable activities with the potential of halving the carbon emissions and decreasing operational costs.
Bystronic is a globally leading technology company that supplies high-quality solutions for sheet metal processing. By nature, sheet metal processing is resource- and emission-intensive. Machines must be durable and powerful to bend and cut metal sheets for decades, and the use of such machines requires significant amounts of energy.
The project at a glance:
- Bystronic wants to decarbonize the resource- and emission-intensive processes of sheet metal processing with a new generation of bending and laser cutting systems.
- Based on the findings of a life cycle assessment, Bystronic and Zühlke identified four focus areas and transformed the insights from the analysis into actionable activities.
- Optimizing resource utilization, embracing circularity strategies, and aligning with genuine client needs resulted not only in a potential carbon emission reduction of up to 50%, but also in a decrease of operational costs.
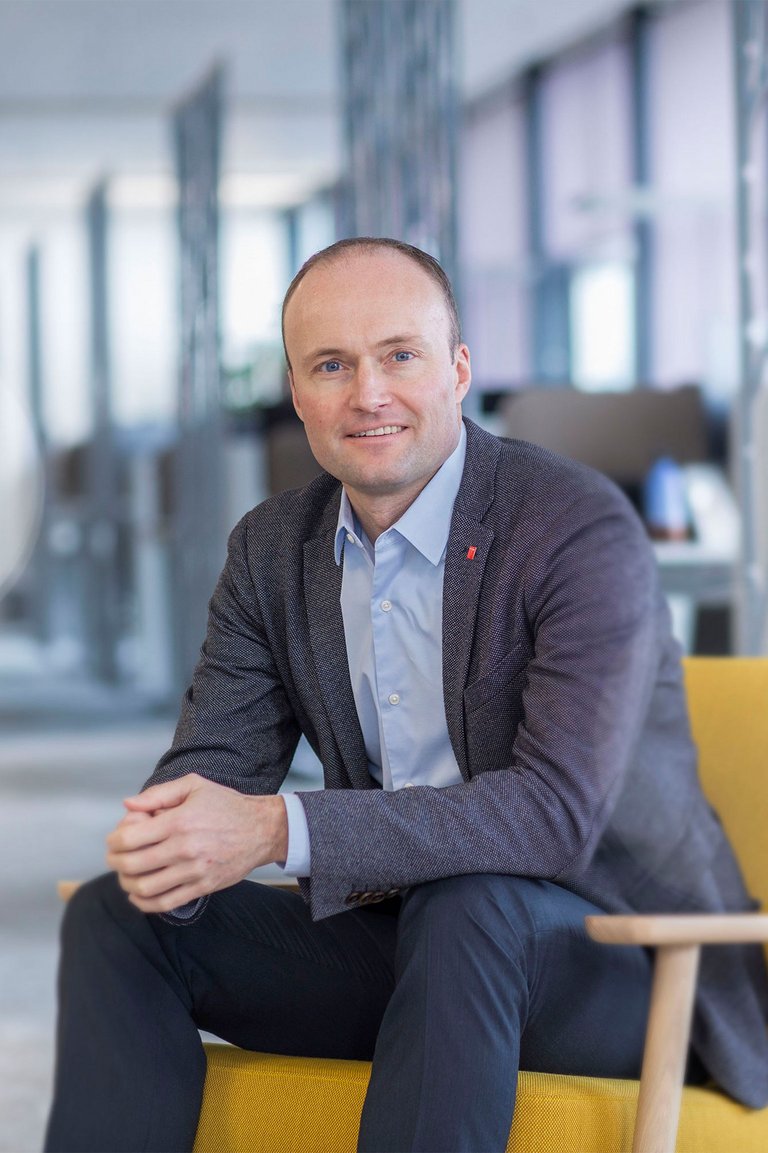
“Our partnership with Zühlke has proven that sustainability and business go hand in hand. Their expertise in sustainability and engineering brought a fresh perspective to our challenges. Our transformation journey is not just about reducing emissions, itʼs about innovating for efficiency and lower operating costs.”
Christoph Rüttimann
Chief Technology Officer (CTO) Bystronic Group
Life cycle assessment as a basis for the sustainability transformation journey
As a first step of the transformation journey, the team evaluated the status quo. We conducted a life cycle assessment of the bending and laser cutting solutions to identify the largest emission drivers. Next, we mapped them with the key parts and functions of the machines based on our sustainable product innovation approach. The analysis revealed some anticipated, but also some surprising insights. While the significant potential of reducing steel and electricity consumption was expected, the unexpectedly high impact of nitrogen consumption on CO2 emissions was quite surprising.
“Zühlkeʼs contribution to our mission of decarbonizing the metal processing industry has been invaluable. Their comprehensive life cycle assessment laid the groundwork for our sustainability initiatives, uncovering significant opportunities for CO2 reduction”, says Bystronic’s CTO Christoph Rüttimann. “Thus, weʼre not just making better machines; weʼre creating a sustainable future for our industry and our clients.”
Meeting sustainability goals and ensuring client focus
In a series of collaborative workshops, Bystronic and Zühlke engineers brainstormed alternative engineering solutions that would help enhance the products’ sustainability, lowering the carbon emissions and incorporating circularity aspects while preserving key functionality valued by Bystronic’s clients.
Within this process, the team identified four focus areas and prioritized them according to their technical feasibility and carbon reduction potential. Following that, the first of several customer value analyses was carried out to ensure a clear customer focus in addition to achieving the sustainability targets.
50% CO2 emission reduction creates real and ongoing business value
By conducting a more thorough study in close collaboration with Bystronic, we converted the insights of the analyses into actionable activities. Optimizing resource utilization, embracing circularity strategies, and aligning with genuine client needs resulted not only in a potential carbon emission reduction by up to 50%, but also in decreasing operational costs.
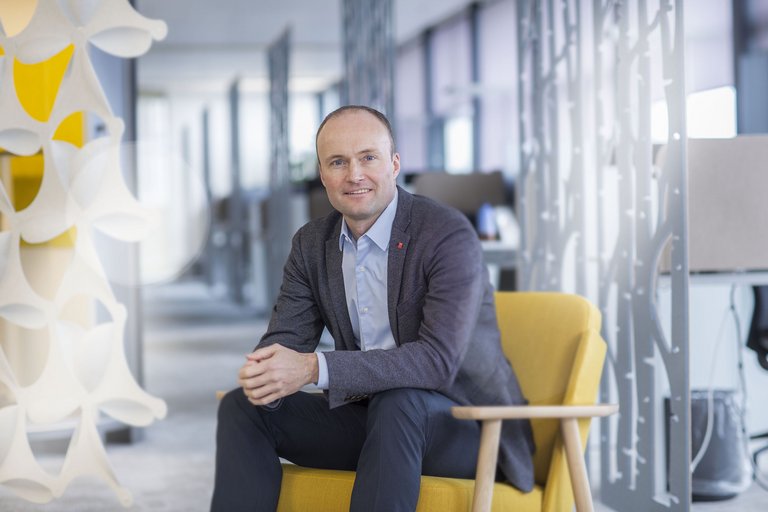