Smart Manufacturing
Smart Factory sets industry benchmark
The future of sheet metal processing begins in Hapert near Eindhoven (NL). There, the company VD Leegte Metaal is building a Smart Factory together with Bystronic. Toine van de Rijdt, CEO of VD Leegte, talks about 99,5% waste free cut parts, the integration of machines from different manufacturers, and his vision for the future.
Mr. van de Rijdt, if you reflect on the smart factory project. How important is it and why?
The smart factory project is one of our top priorities. In the current economy we need to ensure that we meet the demands of the market. Demand is very high at the moment. At the same time we are struggling with a lack of personnel. The smart factory gives us the opportunity to fully automate every step in production. This allows our staff to focus on more challenging tasks. One goal is to do more with the same personal capacity. Currently it is difficult to recruit staff. And that's unlikely to change in the future.
What other goals do you want to achieve with the smart factory?
With this project we want to avoid dual track in the office. At this moment we are working with the IT department of Bystronic and VDL [the parent company of VD Leegte Metaal] to ensure that our ERP System will communicate with the shop floor and also to shop floor back to our ERP system so that there is a connection between it and we don't do things twice. Furthermore we need to ensure that all data is immediately copied in both systems.
Where on the shop floor does the Smart Factory increase efficiency?
Many processes will now run fully automatically. Things will go faster everywhere. Material handling, for example. We are building a big sheet warehouse with 1400 cassettes. With this fully automated warehouse we eliminate a lot of logistical activities that was previously done by a laser operator. This saves us a lot of time, which we can use for more productive work.
What is the material handling process on the laser cutting machines?
Every laser cutting machine comes with a sorting solution. All the cut products are automatically sorted on the pallets. We have also two robot bending cells. The cut parts go directly to the bending machine so that we can produce 24/7. Everything from laser cutting, sorting, bending and the logistics of our warehouse is fully automated. The transport between the machines and the warehouse is ensured by AMRs, logistics robots.
What fascinates you personally about the smart factory?
From my point of view, a big step forward is that the staff is relieved of heavy work. And automating the current processes is just the beginning. Automation steps are also pending in welding. Beyond that, I'm intrigued by the many possibilities that the data we collect gives us. We can now monitor performance of the processes in real time and can optimize production promptly if necessary. The smart factory enables us to initiate improvement processes. Last but not least, I’d like to mention the integration of machines from different manufacturers into an overall production process.
What do you think will change in terms of working dynamics by introducing the Smart Factory?
One thing is certain: the changes are huge. In future the operators have to ensure, that the machine remains free of errors, and the machines are kept in production by means of the shop floor software and plant planning. So the priority is preventive maintenance. In a smart factory we also need other types of personal.
And how is the organization of production changing?
From planning to production, processes today are generally step by step. With the data we have today, we can plan and run processes much more efficiently. We always have the possibility to find the best solution in real time,depending on the orders we can switch.
What is your vision with this factory in the future?
Everybody talks about industry 4.0. But actually there’s a long way to 4.0. I think we have 2.0. the next steps are that we are going to make also solutions online that our customers can easier make their purchase order and that our production knows directly what it must do. So we will connect the customer from our customers in our system. I also see a lot of potential in welding robots. Together with universities and suppliers, we are working on new solutions for the welding process step.
New solutions have also emerged through the cooperation with Bystronic.
That's right. In 2020 we bought the 12 Kilowatt Fiber with a automatically sorting solution. This basically worked well. We are happy with it, except for the residual waste that can be generated when cutting certain parts. If the cut parts still pass through the hands of employees - make sure that no residual material goes on the pallet with them. If automatic sorting is used, this quality control is missing. Therefore, we demanded that this residual waste be reduced to an absolute minimum. So we made a co-development agreement with Bystronic to reach waste free products.
Has it been possible to reduce residual waste?
Yes – 99.5% of the products are now waste free. Bystronic developed a two-stage process for the BySort that separates product and residual material. The solution consists of vibration tools and a tilting table. That's one of the co-development innovations. Another innovation revolves around the cleaning of the grids. We would like to be able to do it without people for this work step as well.
What do you think, in general, about co-creation?
It's very important because by joining the forces form all the companies, you become stronger and smarter together. And by knowing what each other wants and what the knowledge is, you come the best solutions.
What is your conclusion so far on the corporation with Bystronic?
In general, we are very satisfied with the corporation. Bystronic has two project leaders on site. They communicate well and response times are very fast. At the moment we discuss a maintenance contract when we get the keys on 1 of April 2023.
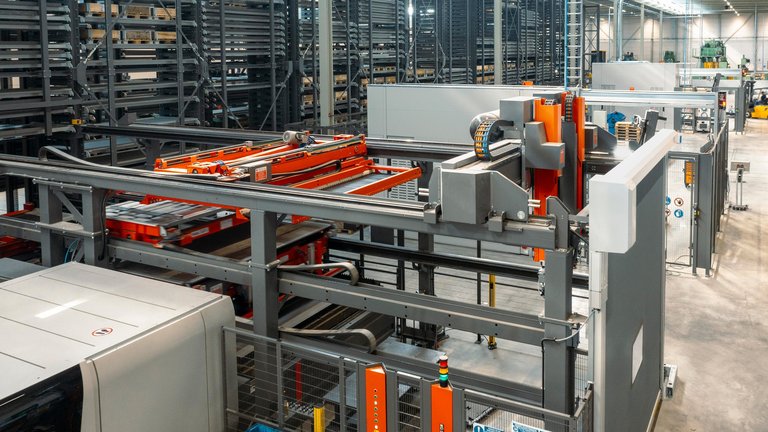
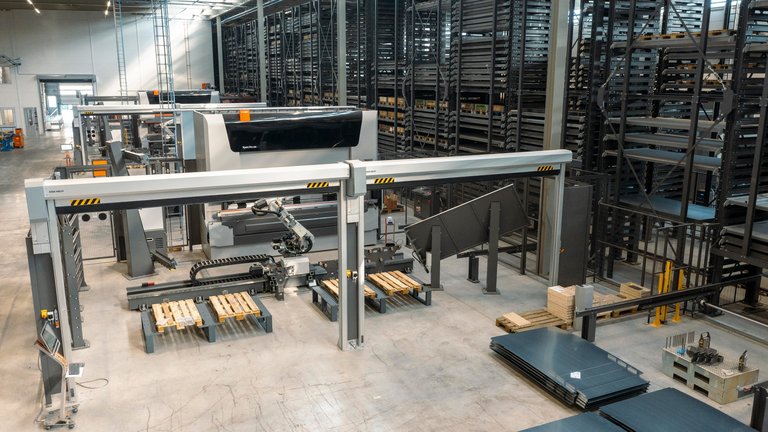
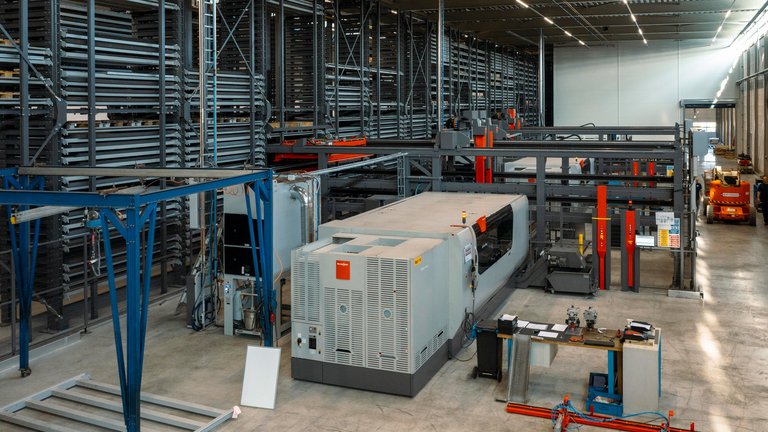
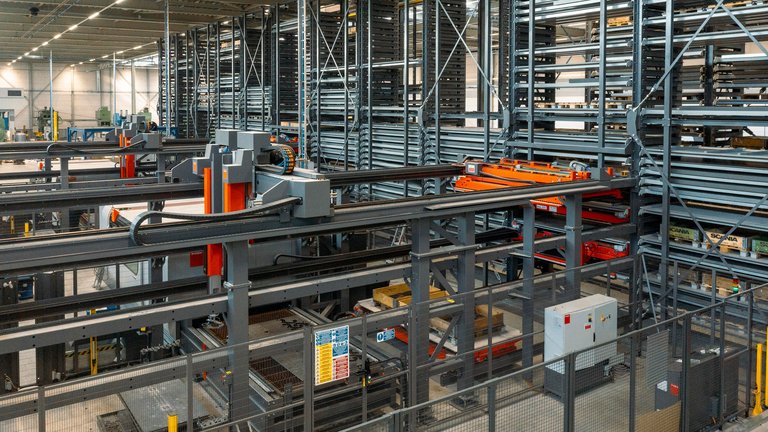
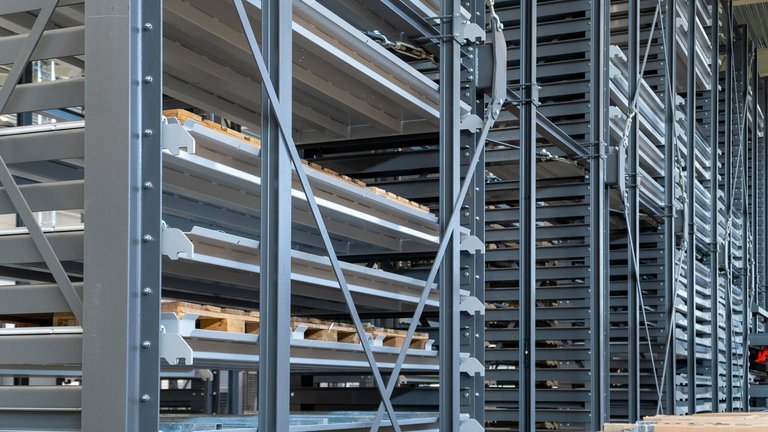
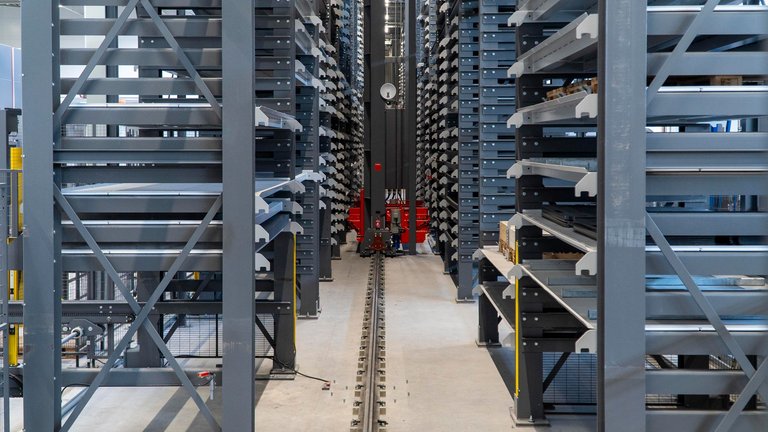
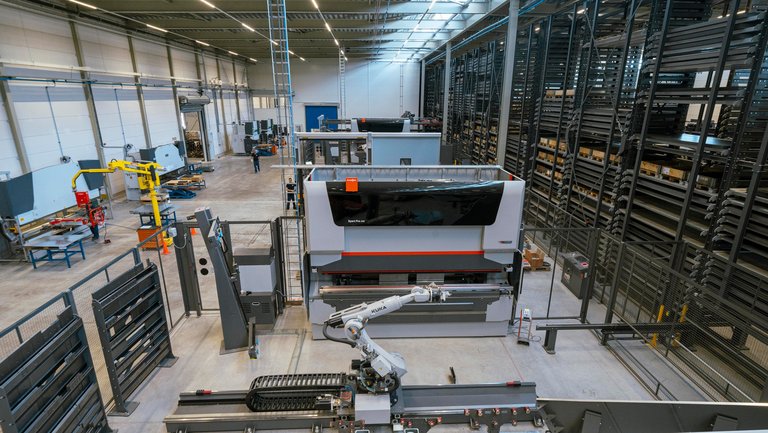
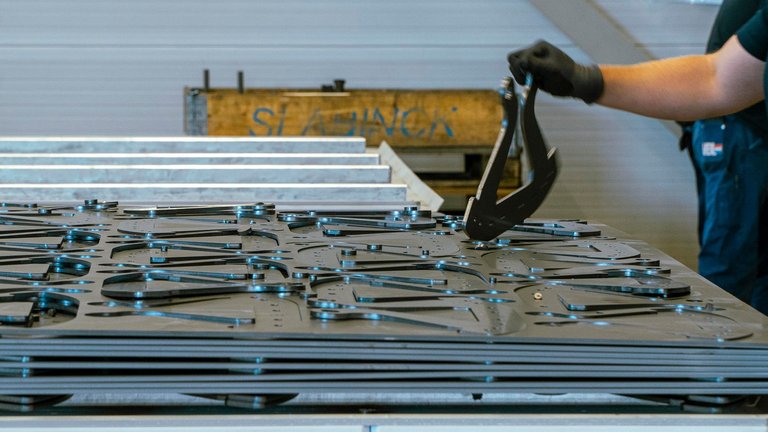
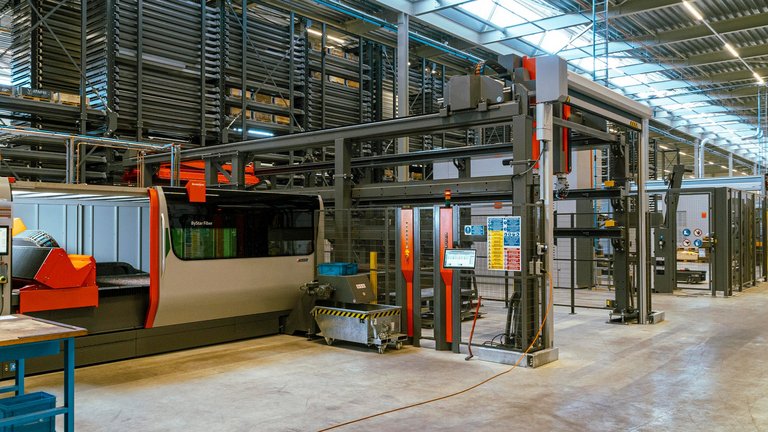
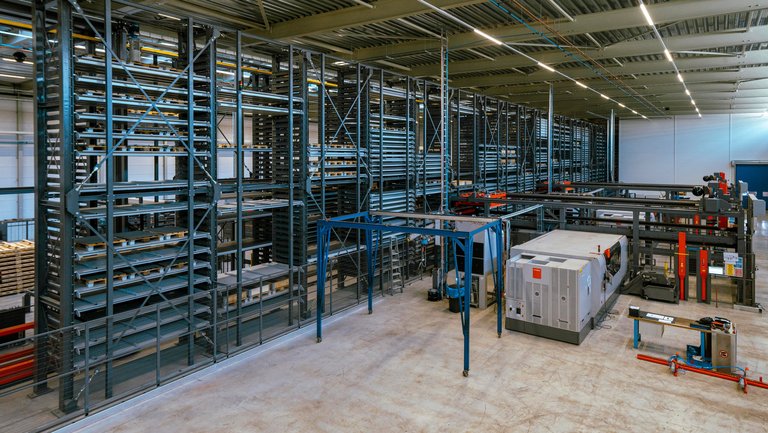
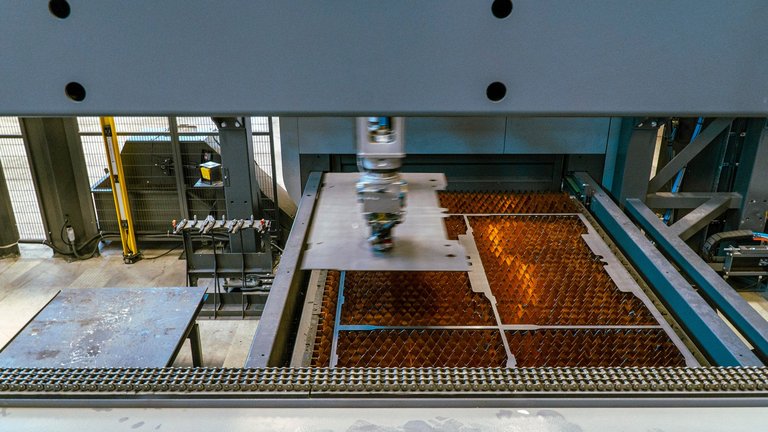